Get Your Silicon Substrate Quote FAST!
Buy as few as ONE Silicon Substrate Online and SAVE!
There are so many different applications for silicon substrates, it can be hard to know where to start.
Below a researcher required a quote for the following substrate.
"We need Silicon substrate with 20nm
SiO2 layer. Do you have this
sample. If not please tell me
what is the closest thickness
do you have for oxide layer?"
For specs and pricing reference #214979.
UniversityWafer, Inc's have a wide range of silicon substrates, we have the perfect option for every application. Our substrates are available in a variety of sizes, shapes and performance levels so you can find the perfect fit for your needs.
Silicon substrates are mainly used for power semiconductors in automotive, electronics and HF front-end pa. silicon that can be fused with other materials, such as thermal oxide and or silicon nitride.
Silicon Substrates Availability
Buy your substrates online and save!
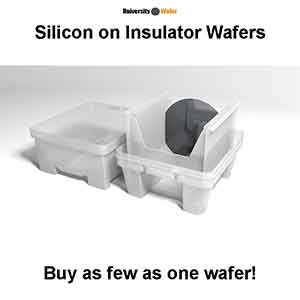
Thermal Oxide on Silicon Substrate
Wet and dry thermally grown oxide available. Wet grows on both sides of the wafer by default. Dry oxide can be grown on just one side and can be less than 200nm. Buy SiO2 coated silicon substrates.
Silicon Nitride (SiN) on Silicon Substrates
We have the following nitride growth methods:
LPCVD Stochiometric
Low Stress Nitride
Super Low Stress Nitride
PECVD Nitride
Metal Deposition on Silicon Substrate
Metallurgical metal deposition techniques on semiconductors include three basic processes: galvanic displacement, substrate catalysis, and autocatalytic deposition. Generally, the galvanic displacement is commonly used to deposit Ag or Cu on Si. Below are the three main processes of metal-on-Si deposition.
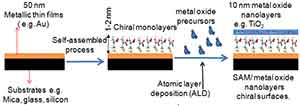
In order to produce electronic devices, a silicon substrate must be covered with metal. Metallization is the process of connecting circuits. In this process, metallic thin-films are deposited onto the wafer to form conductive pathways. Common metals are copper, nickel, chromium, gold, and germanium. Selected metal alloys such as tantalum and platinum may also be used. Vacuum deposition methods are employed for this purpose, including sputtering, electron-beam evaporation, and filament evaporation.
The first step in the process is to deposit a buffer layer of Si. The Si layer was deposited at 550degC on a 0.01 cm (100) n-type silicon wafer. After the buffer layer is deposited, hydrogen stabilization is used to clean the surface and anneal the wafer for 30 minutes at 850degC. This step is known as epitaxial growth.
Send us your specs and quantity for an immediate quote.
Why Silicon is Used As Substrate in Electronics?
The answer is actually quite simple - it's because silicon has a high-gloss surface. The float zone, where crystals are aligned, is the conductive region of the silicon substrate. This enables the device to work in a low-power environment, a critical factor for solar applications. And, it's extremely difficult to cut a crystalline silicon wafer without damaging the entire substrate.
Unlike other materials, silicon is not a strong conductor or insulator. Nonetheless, its abundant supply makes it a more desirable material. This means that silicon is used as a substrate in electronics. In the electronics industry, the semiconductor is called a silicon wafer. It is also a common material for computer chips and microchips. Besides, silicon is cheaper than other metals, such as germanium, which can make it harder to chip.
The most common material for silicon substrates is a silicon wafer. These are super-flat disks with very tiny irregularities. As a result, they are the most reflective object on earth. There are several ways to manufacture a silicon wafer, including the vertical bridgeman method and the Czochralski pulling method. In addition to this, it is easy to cut a silicon wafer. There are two main methods of fabrication: horizontal and vertical.
What is a Silicon Substrate?
Silicon substrates/wafers have many uses, ranging from micro-fabrication to thin film research. They are also useful as biological substrates. They are packaged in a wafer carrier tray or on a disc with a wafer adhesive. The adhesive sheet makes the silicon chips easier to remove, reducing waste and ensuring a uniform surface. Moreover, micro-tec silicon wafer substrates are a useful flat medium for SEM imaging.
Si wafers are the basic building blocks of modern semiconductors. These thin disks have mirror-like surfaces and no micro-particles, making them the ideal substrate material for modern semiconductors. Various methods are used to process silicon, including Czochralski pulling, Float Zone (FZ) growth, and horizontal gradient freeze. Here are some of the common ways to fabricate silicon wafers:
What is a Substrate in Silicon?
Silicon wafers are the most commonly used substrate materials. They are made from a super-flat semiconductor material, with tiny irregularities on the surface. The flat surface is the most reflective object on earth, making it the perfect substrate material for modern semiconductors. They can be manufactured using several methods, including the Float Zone (FZ) growth method and the Czochralski pulling method. The first method is the simplest and is often used to fabricate a silicon wafer.
A silicon wafer is a super-flat disk made of silicon with subtle surface irregularities. A silicon wafer is the flattest object in the world, and is free of all micro-particles and impurities, making it the perfect substrate material for modern semiconductors. The second method is the most complex, and uses a combination of two different methods. In this method, a wafer is sliced into smaller rectangular blocks, called a chip.
The second method involves doping the material to change its electrical properties. The first is the P-type silicon wafer, while the latter is the N-type silicon wafer. The former is the more common of the two types, while the latter is the negative of the two. In a semiconductor, a positive substrate is called a P-type semiconductor while a negative one is referred to as an N-type.
The primary flat is the most important of the two types of flats in a silicon wafer. It is the longest flat of the wafer, with a specified crystal orientation. The secondary flat is the next one, and is the second. It is the most important type of silicon substrate. While its purpose is to enable semiconductors, it is the main component in electronic devices. Its advantages outweigh its disadvantages, and it is the perfect substrate for modern semiconductors.
A silicon wafer is a thin slice of silicon material. It is used in electronics for the fabrication of integrated circuits, while in photovoltaics it is used for conventional solar cells. Since silicon is the 2nd most abundant element on earth, it is an essential component of almost every modern electronic. It can be processed by several methods, including Czochralski pulling and Float Zone (FZ) growth.
The primary flat is the longest flat of a silicon wafer, indicating the crystal orientation. Secondary flats indicate the doping and orientation of silicon. The primary flat is the most common type of silicon wafer, while the secondary one is the most expensive and has the least mobility. It is used in the fabrication of microchips and chips. ICs are the key component of modern electronic devices. These devices need a silicon substrate for their manufacturing.
The float zone is the smallest part of a silicon substrate, with a high-glossy surface. Float zone is a region where the crystals are aligned. The Float zone is a conductive region that allows a device to function in a low-power environment. This is important for solar applications. However, it is difficult to cut a crystalline silicon wafer.
The silicon wafer is a thin slice of silicon. It is an essential component of many electronic devices. It is the second most common element in the universe. The silicon wafer is a highly pure finished product. The crystalline silicon in a wafer can be used to make any electronic devices. If you're looking for a semiconductor, a wafer can be very useful. It can be a source of power, or a source of energy for a battery.
In semiconductors a silicon wafer is also referred to a silicon slice and silicon substrate. Think of a substrate like a wall which can be painted on, or wall papered. It's the base for which microelectronics are etched onto the surface.
Each silicon substrate diameter has a semiconductor standard thickness. For example 100mm silicon substrate standare thickness is 550 microns +/-25 microns. Crystalline silicon (c-Si) subsrate is processed into Integrated Circuits (ICs) and solar applications. The silicon substrate is the base used to fabricate micro-electronic devices on the surface.
The steps to make a silicon subsrate chip includes:
- Doping
- Ion Implantation
- Etching
- Thin-film deposition
- photolithographic
All specs in stock
We have as thickness as thin as 5-25 micron in stock
Single and double side polished available.
Orientation rang from (100) (111) and (110) and other that are hard to find, we have!
Hard to find diameter in stock.
P-type and N-Type available.
Boron doped, phosphorous doped, arsenic doped, antimony doped and undoped available
FOBS substrate carrier available.
We have thin silicon substrates that are as thin as 5um. More commonly we have 50-100 micron in stock.
What Substrate is Used for Neural Platform Research?
Research Paper: anoelectronics enabled chronic multimodal neural platform in a ouse ischemic model
Despite significant advancements of optical imaging techniques for mapping hemodynam-ics in small animal models, it remains challenging to combine imaging with spatially resolved electricalrecording of individual neurons especially for longitudinal studies. This is largely due to the stronginvasiveness to the living brain from the penetrating electrodes and their limited compatibility withlongitudinal imaging.
"The multi-layer probes were fabricatedusing photolithography on a nickel metal release layer depositedon a silicon substrate (900 nm SiO2, n-type 0.005 V cm, UniversityWafer, Inc. MA, USA)."
Please contact us for specs and pricing.
What are Silicon Substrates?
There are many things made of silicon substrates, including computer chips and smartphones. Silicon wafers are the most common substrates, and are extremely flat disks with very tiny irregularities. Silicon is the most reflective object on Earth. Silicon wafers are manufactured by several methods, including the vertical bridgeman method and the Czochralski pulling method. Wafers are then cut with a variety of methods. The resulting chips are then used to make semiconductor devices such as computers and cellphones.
Metals can be deposited on a silicon substrate in a variety of ways. For example, a silicon substrate may be covered with a thin layer of silica or silicon nitride. This process, known as metallization, involves the deposition of metallic thin films on the silicon wafer to create conductive pathways. Common metals include copper, nickel, chromium, and gold. Vacuum deposition techniques can be used to deposit the metals.
Silicon is an element in the earth's crust. It is the eighth most abundant element in the universe. It is less reactive than other elements, including carbon and germanium. Silicon is found in varying forms in the environment, but rarely occurs as a pure element. Instead, it is commonly found in the form of silicates and other compounds. However, silicon has other uses. Silicon is used in the manufacture of computer chips, in which silicon wafers are grown by the Czochralski process. This process takes one million hours to complete.