Whare are Fused Silica Properties
Fused Silica glass is pure silicon dioxide (100% SiO2) in the non-crystalline state, as well as silicon dioxide in the organic state and silicon oxide in the liquid state (in this case a liquid). Fused Silica is difficult to fabricate and thus costs more than all the other glasses.
It can withstand short-term operating temperatures of up to 1200 degrees Celsius and is suitable for a wide range of applications such as solar cells, solar cells, batteries or even medical devices.
Below are the transmission curves of JGS1, JGS2 and JGS3.
Buy online and save! Or, send us your specs/qty for an immediate quote.
Get Your Quote FAST!
Fused Silica Tranmission Curve
Below are the grades of fused silica.
JGS1 Fused Silica

JGS2 Fused Silica
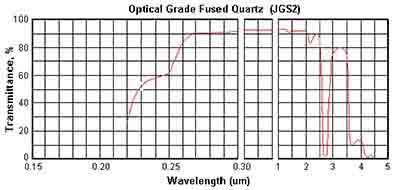
JGS3 Fused Silica
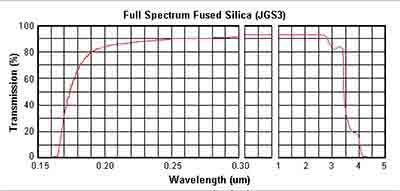
What is The Eplsilon_r (Permittivity) of Fused Silica?
Substance |
Dielectric Constant(relative to vacuum) |
LossTangent |
Fused quartz |
3.8 |
0.0002 @ 100 MHz |
0.00006 @ 3 GHz |
What Is Silica Glass?
The most common question that asks what is silica glass is the definition. It's a clear and strong material formed from the fusion of pure silica at very high temperatures. Many applications use glass in their optical instruments. In this article we'll look at the different types of silica glass, the properties of these materials, and how they're made. Read on for a more detailed explanation.
Silica glass has numerous applications. It is often used in the fabrication of high-tech items. It is used in furnace core tubes, wafer boats, masks, and other components in the semiconductor industry. It is also a common component in optical fiber manufacture, including window panes for ultraviolet and infrared light. It's also used in high-lumination lamps. And that's just the tip of the iceberg.
Although silica is common throughout the earth, its purity varies widely. Geyserite, found in Iceland, is used to produce the highest grades of fused silica glass. This glass is so pure and durable that it's used in space craft and deep sea submersible crafts. Even astronauts use it to fabricate windows on the International Space Station. If you're interested in learning more about the properties of silica glass, you can learn more about its uses.
Among the many different types of silica glass, the most common is quartz, which is a crystalline solid that closely resembles glass, but exhibits unique characteristics. It's also very rare and has limited industrial uses, but quartz is perhaps most familiar to us as an electronic component in watches. Another type of silica that is often used is fused silica, which is a glassy substance that is produced by melting natural crystalline silicon. The difference between these two types is the fact that fused crystalline silica is much more transparent and contains no additives.
A good example of silica glass is quartz, which is a type of quartzite that is naturally occurring. The natural form of the mineral is a crystalline solid that has many distinct properties, but it still resembles a glass. The most commonly used type of fused silica is the most expensive type, which is derived from a quartz crystal. Moreover, this type of silica is used in spacecraft and deep sea submersibles.
There are many types of silica glass. The main type is quartz, which is a crystalline solid with distinct properties from that of a liquid or a solid. This type of silica is used for quartz crystals in electronic systems, and you may have seen them in your wristwatches or other gadgets. There is also fused silica, which is a synthetic form of silica. This is a glassy amorphous solid that contains no added substances and is very durable.
Soda-lime glass is the most common type of silica glass. It is a type of non-crystalline silica and is made by melting natural crystalline sand. Soda-lime is a very pure form of the material, and is often used to make a variety of products, including windows and mirrors. As with all kinds of glass, however, it can be tempered to increase the durability of its properties.
Silica glass is a common substance that is used for many applications, including windows in buildings. In addition to being a useful construction material, silica glass is also used to make automobile windows. While both materials are incredibly hard, quartz crystals are considerably softer than regular glass. It's impossible to scratch quartz, so its use in a building is vital for the safety of its inhabitants. So, the answer to the question, "what is silica glass?" is very simple.
Silica glass is a material that is used to make flat, transparent glasses in buildings. It is also used in the production of car windows. While the two materials are similar in chemical composition, they differ in their hardness. In the Mohs scale, glass is a soft material. In contrast, quartz is a very hard substance. Its surface will scratch any object it comes in contact with. So, how is it made?
What is the Chemical Composition of Fused Silica?
Fused silica is a specialty material. It is glassy and low in hydroxyl
content. Though it is sometimes mistaken for water, hydroxyl is not the same as water molecules. IR grade fused silicas should have a hydroxyl content below 10 ppm. The wavelength of hydroxyl content is between 2.2 mm and 2.7 mm. The overtone bands are in the 1.4 - 1.5 m region and are relevant for telecom wavelengths.
Although quartz and fused silica are similar in chemical composition, their structure differs. Quartz is fabricated by fusing powdered crystals in a hydrogen-oxygen flame, while fused silica is manufactured by flaming silicon halide in a furnace. Both types of glass have different purity levels and applications. For example, the quartz in this type of glass is commonly used in lab equipment and UV windows.
Fused silica is a noncrystalline form of silicon dioxide. This means that its atomic structure is not long-range ordered. It has a highly cross-linked three-dimensional structure, which makes it ideal for high-temperature applications. Additionally, fused silica is highly resistant to heat, and it has a low thermal expansion coefficient. Despite the differences in atomic structure, fused silica is used in fiber optics, electronics, and optical equipment.
Unlike quartz, fused silica is made by fusing powdered crystal quartz in a hydrogen-oxygen flame. This process yields a crystal with high purity and low density. Moreover, this glass is also highly resistant to ultraviolet light, making it a valuable material for optical components. It is also used in precision mirror substrates, semiconductors, and laboratory equipment.
The most common uses for fused silica are in semiconductor devices. FTIR and Raman spectroscopy are the most common methods to measure the OH content in fused silica. However, there are a few other applications where this glass is not so suitable. It is commonly used in the space shuttle and deep sea submersible craft. If it is a high-quality material, it is inert and non-reactive.
In addition to the advantages of a high-quality product, the chemical composition of fused silica is important to the process of manufacturing. The high OH content of the material makes it a great choice for optical components. For this reason, it is the preferred material in biomedical equipment. Besides being strong and transparent, it is also chemically inert. Its low thermal expansion and elasticity make it suitable for a range of applications.
Fused silica is one of the few types of glass that is not crystalline. It is made from silicon dioxide and is a form of silicon dioxide. It is an inert material that is highly resistant to temperature changes. In contrast, other forms of glass are not temperature-resistant and do not melt at all. The material is more flexible and can withstand high temperatures. When heated, however, it exhibits perfect brittle-elastic behavior.
When used in optical components, fused silica is also useful for other applications. Its high sensitivity to light, high transparency, and low thermal expansion make it desirable for large telescope mirrors. In addition, it is highly durable and resistant to extreme conditions. It can even be used as a photomask. And since its thermal expansion properties make it ideal for optical windows, it can also be utilized as a solar panel.
Fused silica is a noncrystalline form of silicon dioxide. It is a three-dimensional material that is highly cross-linked. Because of its unique structure, it is a good thermal insulator and can withstand high temperatures. It is also useful in optics for its high-temperature resistance. Its thermal expansion coefficient and broad spectral range make it ideal for a wide range of optical components.
Fused silica is a form of quartz. The chemical formula for this material is SiO2. The most common type of fused silica is pure-silica. In contrast, quartz is a combination of pure-silica and fluorine. The latter type is called amorphous, and is more transparent than the former. So it is more likely to be used in optics.
What is Fused Silica Glass Composed of?
Fused quartz glass is a combination of quartz glass plates having special properties and is known to be one of the best alloys on earth. This combination of minerals is developed through the heating process by which the silicas are fused together. The heated quartz glass plate is then used for making the lens. The cooled fused silica crystal is then formed as the bottom portion of the lens. During the process, the strength of the structure is improved and the transmitted light is sharper.
Parallel Split Lens Configuration
The high transmission range is obtained due to the jigs model which was developed as a parallel split lens configuration. The jigs are made up of two parallel glasses with a gap between them. Through this, the transmission range increases considerably. The high transmission range along with the finer transmission lines lead to improved image sharpness.
Video Split Lens - Jee Problem
How do you Make Nano-Lithography (NCL)
Fused Silica coupled with Silicon and Magnesium produce a compound referred to as Nano-Lithography (NCL). This is another micro-fabrication method which is used in the manufacture of many micro-optic devices including mirrors. This system produces ultra-thin, highly accurate mirrors. The optics associated with this type of fused silica mirror is said to be better than any other known micro-fabrication technique. It utilizes small crystals or glass materials to create an extremely thin, highly-precision micro-mirror thereby enabling transmission of light at virtually high speed.
Video Electron Beam Lithography Nanofabrication Techniques
Can Micro-Fabricated Mirrors be Used for Optical Wave Shaping Applications
A major deficiency of this type of mirror is its inability to change the transmitted wavelength of light into any of the other six major wavelengths. Hence the micro-fabricated mirror cannot be used for optical wave shaping applications. The main optical function of this type of mirror is to modify the transmitted wavelength into any of the six major wavelengths. This enables the mirror to emit light of any desired wavelength at a high optical efficiency. Since the main limitation of this type of mirror is related to the wavelength of light transmitted, the invention of nanofabrication techniques has been employed to increase the ability of this device to alter the transmitted wavelengths. In particular, by placing shorter wavelengths in the focus of the fused silica crystal, it is possible to increase the ability of the device to change the focus.
Video Micro Mirror Arrays
What are the Major Components of Fused Silica?
The major components of a quartz crystal are silicon (Silicon (III)) and phosphorus (phosphorus vacancy filter (N phosphate)). Both these components play significant roles in quartz crystal structure. However, the quartz crystal structures are highly complex and involve many parameters like the mode of crystal lattice (monochromatic) or dimorphism (dipstick) among others. These parameters determine the crystal size, crystal quartz (which gives mechanical tension to a crystal component), mode of internal diffusion (absorbed into the lattice) and absorption in infrared. The quartz crystal structure is dependent on the mode of transmission and the frequency of transmission.
It is interesting to note that the mode of transmission spectrum within the UV range is not fixed. There are three modes of transmission spectrum within the uv range i.e., near, mid and far transmission spectrum within the range. Thus, there is a wide range of frequencies and wavelength within the UV range. This is why fused silica can be used in different applications.
The mode of thermal expansion (T ERF) is basically the transmission spectrum of a crystal lattice. The lattice structure is considered as a reflection of thermal contraction and thermal conductivity. The thermal energy is trapped inside the crystal structure during the T ERF process. The electrical field is emitted outside of the crystal lattice during the non-thermal breakdown of atoms.
The optical transmission and the thermal expansion within the quartz glass include distinct features. As the optical transmission is a two-dimensional optical waveform. Thus, the spectrum of thermal expansion is also two-dimensional. Thus, fused silica can be utilized for both types of optical transmission spectrum. In addition to the optical transmission, the fused silica can also be employed for the thermal transmission.
What Fused Silica Properties Do I Need?
Silicon dioxide, an industrial raw material, is used to manufacture many thermal processes at high temperatures, including steel, investment casting and glass production. A wide range of products are available from sand and rock crystals, which are produced by fusing naturally occurring crystalline silicon. Silicon dioxide is made from a variety of materials such as sand, rock, sandstone, gravel, clay or sand. [Sources: 1, 3]
These materials include materials for use in the ultraviolet and infrared ranges, which are used in a wide range of applications such as high-resolution imaging and optical imaging. Heraeus and Nikon produce a wide range of silica glass melting products for consumer and industrial applications, all of which have excellent ultraviolet or infrared performance. [Sources: 7, 8]
Synthetic silicon melts are able to make their grade suitable for a wide range of applications where other materials are not suitable. Due to their very low coefficient of thermal expansion, they can be heated, cooled and cooled and withstand temperatures of up to 950 degrees. dpa This allows them to be used as electrical, thermal and insulating materials in wide areas of the environment, as well as for high-resolution imaging and optical imaging. [Sources: 2]
The quartz glass also has excellent thermal and shock resistance, and when heated to 1100 degrees Celsius and maintained at this temperature for about an hour, the fused quartz glass changes color. If the material is heated to 1100 degrees Celsius, then suddenly rolled up and cooled down to 20 degrees, a piece of it can be broken off, then the procedure is repeated three times. [Sources: 4]
The synthetic grade Fused Silica is able to display water vapor uptake in the near infrared. In contrast, IR-compatible quartz glass contains much less water traces and shows significantly lower absorption into infrared light. Water vapours, for example, create a much more visible pattern of light traces on the glass surface. [Sources: 0]
Molten quartz can undergo large and rapid temperature changes without cracking, and therefore low hydroxyl quartz material manufactured by Momentive Performance Materials has the advantage of being resistant to grease. Precise measurement transmission enables quartz glass qualities to be produced from various types of sand, mountain and crystal. [Sources: 5, 7, 9]
Silicon dioxide is extremely strong under compression and its wide transparency range ranges from UV to almost IR. Its properties make it ideal for applications that require high resolution, low cost, high performance and high transparency. Quartz glass can also be fused in a variety of applications such as solar cells and solar cells. Due to its high thermal conductivity and low thermal resistance, it is also very well suited for use in the solar industry. [Sources: 0, 1, 9]
The most important chemical factor influencing the sag strength of fused quartz is the hydroxyl (OH) content. The optical properties of quartz glass are much better than those of standard glass, because quartz glass has a much higher degree of purity. The most common contaminants are those that can influence the transmission behaviour of quartz, such as water vapour, carbon monoxide (CO) and nitrogen oxides (NO). The reason for the different transfer behaviour is the composition of quartz and its chemical composition as well as its optical and thermal conductivity. Its optical properties depend on the presence or absence of a number of impurities - free materials and other factors. [Sources: 4, 5, 7, 9]
When hydrogen is actively charged into the molten silicon dioxide, the free hydrogen content of the material can exceed that of a standard glass, such as quartz glass, due to the presence of hydrogen. [Sources: 9]
Silicon dioxide is superior to other types of glass in its purity and opens up new areas of application. The variety of applications for used silicon and quartz melts increases the risk of thermally induced fracture of the materials used in them. Although they are normally used in a continuous process of melting silicon dioxide and the dust that is produced, the molten silicones can be made from almost any silicon - an alternative process can be used to produce a rich chemical precursor. However, due to their high chemical content, they are not integrated into the process, which leads to increased optical transmission of light through the glass and higher optical performance. [Sources: 1, 7, 9]
Young module of silicon that brings in a much larger coating, and there is a significant difference between the molten quartz and the other molten silicones. The manufacturing process determines the temperature and viscosity of molten silicon dioxide and molten quartz, as well as their growth rate. Temperature and quartz viscolysis are the most important factors, but oxygen, water vapour and partial pressure also influence crystal growth rates. [Sources: 1, 5, 6]
Melted quartz fibres require a low OH material, as they must be bent in such a way that they have as little damping as possible over long distances. [Sources: 9]
This results in a complex process in which silica is removed from the quartz fibres and the resulting ash and a highly OH-containing material forms. UV - IR (FS - KS-4V), which combines excellent physical properties and is a good candidate for the production of high-impedance materials. There are a number of different types of fused silicones, such as silicones, silicates and melts with other metals such as copper, nickel or iron. [Sources: 2, 9]
Sources:
[1]: https://en.wikipedia.org/wiki/Fused_quartz
[6]: https://www.ncbi.nlm.nih.gov/pmc/articles/PMC6891625/
[9]: https://www.spiedigitallibrary.org/conference-proceedings-of-spie/10014/100140F/Metrology-of-fused-silica/10.1117/12.2242487.full
Fused Silica Wafers Used for Stress Measurements
When it comes to fused silica wafer specifications for stress measurements, a number of factors should be considered. These include the wavelength of operation and the size of the fused silica window. Ideally, the fused silicon wafer should have a low thermal expansion coefficient and a high use temperature. The following are some important things to consider when selecting a fused silica window.
The first feature to consider is the alignment fiducial. The finducial, or the flats or notches in a glass wafer, will indicate the type of the wafer. The other element, such as the notch or pocket, is a special identifier. Inseto uses the word "other" to describe a wafer that has a patented identifier or is stacked in a specific way.
Is Fused Silica the Same As Quartz?
The terms quartz and fused silica are used interchangeably, but the two are very different materials. Both types of glass are made by melting naturally occurring quartz. While they are both composed of SiO2, they have some differences in their mechanical and electrical properties. These two materials are often used together for the same purposes. Learn how to differentiate the two by reading on to learn about some of the benefits of each one.
First, it's important to distinguish between the two. While quartz is almost entirely silica, fused silica contains non-crystalline silica. These are different types of glass and have different properties. When you're using fused quartz, it will be less crystalline than quartz. In addition, it will be prone to containing trace impurities. Ultimately, it's worth knowing which one is better for your project.
Fused silica is amorphous. This means that it has low levels of hydroxyl, sometimes referred to as water molecules, which is not the same thing. IR-grade fused silica must contain less than 10 ppm. Interestingly, hydroxyl bands are most visible in the 2.2-2.7 mm wavelength region. For the 1.5-mm band of telecom wavelengths, it's best to stay away from this band.
Is Fused Silica Strong?
Fused silica is a strong glass with a high tensile strength and excellent transparency across a broad spectrum of light. It is also resistant to most acids and is chemically inert. Its thermal stability makes it a good candidate for use in biomedical applications. Because of its excellent physical and chemical properties, it is used in many biomedical applications. Its transparency and strength make it a good choice for coating semiconductor devices.
Fused silica's UV transmission spectrum is not fixed. It includes the near-infrared, mid-infrared, and far-infrared bands. As a result, it can be used in various applications. Its fracture toughness value is highly dependent on the fusing process. Some of the methods of fusing enhance its tensile strength. Some of the methods involve the use of special identifiers, like notch or pocket.
In addition to these properties, fused silica has excellent elastic properties, making it an excellent material for motion and micro-mechanical pieces. It is also less susceptible to fatigue than glass, which is a common perception. However, standard fabrication methods lead to microscopic cracks that reduce the tensile strength of glass. In fact, tensile strength is the primary factor that determines whether or not a material is strong enough.
Infrared optics requires a high hydroxyl content. This is sometimes mistakenly called water, but it is a separate substance. IR-grade fused silica must have a hydroxyl content lower than 10 ppm. The hydroxyl content band is around 2.2 mm in wavelength. The overtone band lies in the 1.4-mm region. This band is relevant for the 1.5-mm telecom wavelength band.
Compared to other materials, fused silica is the most flexible. Its density is only 2.6g/cm3, whereas steel, aluminum, and Invar have similar density. Its elasticity modulus is 73GPa at 25oC, which is about double that of steel. Its brittle-elastic properties can be increased by applying different fusing techniques.
The tensile strength of fused silica is 5x10-6 Pa, which is comparable to glass. It is important to remember that the hydroxyl content in fused quartz varies between the two types. The hydroxyl content in raw quartz is higher than that of fused silica. When comparing the two materials, the former is stronger. The latter is the best choice for a variety of reasons.
As a relatively pure material, fused silica has low thermal and chemical shock resistance. It is transparent at wavelengths of 0.2 to 3.5 um, which makes it ideal for optical mirrors and flats. Its low thermal expansion coefficient makes it a popular choice for electronic devices, and its high purity makes it an excellent material for medical devices. When comparing these two materials, be sure to choose the one that meets your needs the best.
Fused silica is one of the most common glass materials. Its high strength makes it an excellent choice for many different applications. Its low-index composition makes it useful in dielectric coatings. It is an ideal material for the construction of windows. It is also used in spacecraft and deep-sea submersible craft. Its transparency makes it a very attractive material to space travelers.
While fused silica is very strong, it is also fragile. Its structure is not permanent, and it will break easily. It is used for solar panels and in photovoltaic cells. It is an excellent material in solar panels. It is also used in a wide variety of other applications. It can withstand extremely high temperatures. Its optical properties are dependent on the type of fusing process, which makes it very suitable for both high-tech and low-cost applications.
When it comes to optical components, fused silica is a good choice. It has an extremely broad spectral range and is very resistant to thermal expansion. It is also used for large telescope mirrors and optical windows. It is also very strong, making it a good material for photomasks. This material is often very expensive. In contrast, it is very cheap and easy to obtain. If you need a high-quality glass, you will be able to find it at a reasonable price.
Is Fused Silica Birefringent?
This article will focus on the properties of fused silica and what they mean for a photonic application. While most fused silica is capable of transmitting infrared light, it can also be degraded by UV radiation. To avoid this, you need to select an optical grade with low levels of hydroxyl. The other important feature is that the crystalline structure must be stable when exposed to UV radiation. The quality of this type of glass depends on its use in the application.
A highly purified form of silica is created by a chemical reaction. A vapor-free plasma flame is used to burn silica tetrachloride (SiCl4). The resulting synthetic silica reacts with oxygen and escapes as HCl. The resulting product is a fine powder that is fused to form a solid. A few characteristics differentiate this grade from BK 7. Both types are transparent an exhibit excellent optical transmission and diffusion blocking.
Optical components made from fused silica are commonly exposed to high temperatures and temperature gradients. The hot envelopes of gas discharge and halogen lamps prevent depositions. For excimer and halogen lamps, the high transmission of UV is undesirable, so they require additional filter glasses. In addition, high-power laser applications often require a high-quality optical material. To make them more durable, it's important to choose the proper crystalline and non-crystalline materials. Fused silica has no birefringent properties.
What are Fused Silicates?
Fused silica is a glass-like material with extremely low refractive index. Its homogeneity and
birefringence values are known the world over. It has a very low coefficient of thermal expansion and transmittance over a wide spectrum. It is used in many applications, from semiconductors to UV light sanitation. These properties make it a popular choice for many applications. To find out more about fused silica, read on!
One important property of fused silica is that it is transparent to a wide range of light, which makes it an ideal material for optics. In addition, it is chemically inert, which is desirable for biomedical applications. Its porous structure is an excellent protective layer for semiconductor devices. Because of these properties, it is used in solar cells, photovoltaic panels, and other applications that require high transmission.
Fused silica exhibit high radiation resistance and high use temperature. However, the high phonon energies of light elements cause strong non-radiative transitions within the glass. While this can be beneficial in some applications, it also has disadvantages. Its low thermal expansion coefficient and low use temperature make it a great material for solar energy. But despite their benefits, it is essential to understand how fused silica is produced to make sure you get the best out of them.
Is Fused Silica Expensive?
What Makes Fused Silica So Expensive? A simple answer to this question is that it is the purest form of silicon oxide. Its properties include a low dielectric constant, superior transmission in the UV and IR spectra, and a high degree of thermal shock resistance. Its crystalline structure allows for a wide variety of shapes and sizes, and it is resistant to heat, non-fluorinated acids, and plasmas.
Fused silica is more expensive than float glass, but it has many advantages. It is resistant to most
acids, except hydrofluoric acid. Because it is a highly transparent material, it can be used in a variety of applications, including optical and thermal transmission. It is also very durable, being highly resistant to heat and fire. It is used in the medical field for its optical properties.
Unlike many other types of glass, fused silica is a crystalline solid that is transparent across a large range of light spectrums. Because it is chemically inert, it is often used in biomedical applications. Its high-quality composition has made it an ideal candidate for new applications. The same properties make it a strong and durable protective layer for semiconductor devices. It is extremely difficult to fracture.
Fused silica is a relatively rare mineral. Its highest-grade forms are derived from geyserite, which is a natural mineral found in the Earth's crust. It is a highly durable substance, and it is used in spacecraft, deep sea submersibles, and in a variety of other products. However, the high cost of the material makes it prohibitively expensive.
How do you Clean Fused Silica?
Before you can use a fused quartz surface, it is important to thoroughly clean it. Generally, you
should soak it in a 7% ammonium bifluoride or 10% hydrofluoric acid solution for at least 10 minutes. Then, rinse it with distilled water or deionized water. Always wear cotton gloves when handling the material. This can help prevent damage to the finish.
Using an acidic cleaning solution will not damage the glass or silica, but it will remove certain components from the surface. Mix 2 parts concentrated sulfuric acid with one part hydrogen peroxide and use this mixture to clean your lenses. This solution will also work well for stubborn organic contamination, especially if you don't want to buy expensive lens cleaners. Make sure to use gloves for this process to avoid contaminating your hands.
The pH level of your cleaning solution is extremely important. High temperatures can speed up the devit process. Using alkaline solutions can lead to stubborn devitrification. To prevent this from happening, use distilled water or deionized water. These solutions have a pH level of 7 and are safe for glass surfaces. You should also avoid using water that contains sulfuric acid, as this will leave alkaline compounds on the surface.
Yes, learn more about Piezoelectric Fused Silica Resonators. See below.
Advances in Micromechanical Systems MEMS resonator technology performance has reached parity with miniaturized timing references of single crystal quartz. The extremely small form factor, batch fabrication ability, and integration opportunities of MEMs have tangible benefits for the current consumer drive for wearable technology and ever-shrinking mobile devices. Until recently the majority of MEMS timing references have used silicon, or thin piezoelectric films. As of today there hasn't been much research into microresonators fabricated from fused silica. It's important to note that fused silica is made of high-purity flame annealed amorphous silicon dioxide. It's physical attributes don't lend favorably for use as a resonant material. Fused silica low internal losses, works with in supports for ultra-sensitive gravitational wave detectors, as well as high-quality macro-scale resonators with quality factors (Qs) over 4 million.
There are many benefits to fused silica, which can make it a great material for a number of applications. For example, it can change its focus due to its long wavelength. In addition, it can be easily and rapidly machined. To learn more about the benefits of fused silica, read on. This article will help you understand its advantages and limitations. But first, let's clarify what it is.
Fused silica is a crystalline solid derived from quartzite. The chemical composition of fused silica is silicon dioxide, and it has different properties from its crystalline form. Its physical properties differ from those of pure quartz, but it still resembles glass. The most common type of fused slica is derived from quartz crystal, and it is used in deep sea submersibles and spacecraft.
High-purity fused silica wafers can be used in high-end devices due to their high resistance to high-temperatures. Furthermore, they are noncrystalline and low-diffuse, which are crucial properties for optical and semiconductor devices. Regardless of these properties, fused silica is a very good material for optical and thermal transmission. The high purity makes them a valuable material for these applications.
The most common applications for fused silica include medical devices, optical lenses, and optical components. These materials are often highly resistant to heat and are highly durable. As such, they are a great candidate for new applications in the field of materials science. They also serve as a protective layer for semiconductors. In the future, this technology can be used in solar cells and other electronics. However, the primary uses for fused silica are in optical and biomedical technology.
Which Conducts Heat Better - Fused Silica Or Quartz?
Both materials conduct heat, but each has unique properties. For example, crystalline quartz has the best resistance to thermal shock, while fused silica has a higher electrical conductivity. While crystalline quartz is better for heating applications, it's also the best conductor of heat. The main difference between quartz and fused silica is how they absorb heat. Both materials are good insulators, but quartz is more efficient at heat transfer than either of the others.
Fused silica is a form of glass, but it is more expensive and does not conduct heat as well as quartz. Because it is a good electrical insulator, quartz is used in many electronic devices. However, it's not a good thermal conductor. This is primarily due to the low coefficient of expansion, which is what makes it suitable for a semiconductor device. Because of its high dielectric constant, fused silica is also an excellent choice for shielding and coating semiconductor devices.
Quartz is a natural mineral. It is transparent in a broad range of light and is resistant to most acids. It's chemical inert, which makes it useful for biomedical applications. It's also extremely resistant to thermal shock, making it a valuable material in high-temperature industrial components. Because of its unique properties, fused silica and quartz can be used in a variety of applications, from medical to high-tech.
Fused quartz glass are commonly interchanged. Fused silica is a form of silicon dioxide that is formed through the melting of natural quartz. Both materials are pure SiO2 with various impurities. Although quartz is the purest form, all other commercial glass is made from SiO2 with added dopants to lower the melting point and modify their optical, thermal, and mechanical properties.
As far as heat transfer is concerned, fused quartz is the superior choice for most applications. Its high transparency makes it a great candidate for biomedical applications. Additionally, it's chemical inert, which makes it ideal for use in a variety of medical devices. These properties make it a great candidate for new applications. Aside from optical applications, it can be used as a protective layer for semiconductors.
While quartz is considered the purest form, fused silica is the more popular material in jewelry. Its high melting temperature makes it the most desirable material for jewelry. It is also used as a heat-conducting element. Its high melting point makes it the best choice for jewellery. In addition to its superior thermal and mechanical properties, quartz is also an excellent candidate for high-temperature semiconductors.
Both types of glass are made of silica, which is amorphous and is the purest type of quartz. Its properties are similar, but quartz is more expensive. For jewelry, it is more durable than a quartz stone. It's often used in combination with fused silica, making it a more versatile material. If you're looking for a glass-related item, you'll find fused silica to be the better choice.
Fused silica is the purer form of quartz. It's made by fusing quartz, which is made of silica. While both are excellent electrical insulators, quartz is better at conducting heat. A quartz glass will retain heat longer than fused silica, but it will also be more susceptible to temperature variations. The best way to distinguish between the two types of glass is to look for its electrical properties.
Fused silica is amorphous and contains impurities. It is transparent in a broad range of light and is resistant to most acids. Because it's more porous, it's useful in biomedical applications, such as in the medical field. It can be used in glass for lenses and solar cells. It can also be molded into complex shapes. Its high melting point increases its costs.
Fused silica is the more expensive material. It's more costly and can't be bent like glass. Its low thermal conductivity makes it a better thermal insulator than quartz, but it's not as good as soda lime glass. For this reason, it's better to use the latter. For a wide range of applications, borosilicate glass is a better choice.
How to Manually Dice Fused Silica Wafers
One of the most frequently asked questions about glass wafers is how to manually dice them. These crystalline materials are used in a variety of applications ranging from microfluidic chips for biotechnology to semiconductor processing. If you're unsure how to slice glass wafers, check out this article and learn how to do it yourself. You can save money and time by manually dicing your own glass wafers.
There are a number of different micromachining processes you can use to create through-via holes in quartz and Fused Silica wafers. Laser ablation and chemical machining both offer a good profile for metallization, but can be tricky with very thin wafers. Using a single-layer KMPR photoresist mask, you can etch glass and silicon up to 30 mm deep. This method is best for thicker silicon and glass wafers.
Manual cleaving is a process of dividing a silicon wafer into several smaller chips. A manual cleaving tool called a FlipScribe has ruled markings for easy scribing. Its vertical and horizontal guides make it easy to handle small samples. Cleanbreak pliers were used to cleave the pieces into tiny chips.
The first step is to manually dice the wafers. Using an anodically bonded silicon/glass wafer, we first used a manual cleaving technique. This technique involves placing an anodically bonded glass/silicon test chip on a glass support with two anchors. The silicon anchors are spaced 500 m from the center line of the glass chip.
Manual cleaving has many advantages. It is the best way to manually dice silicon and glass wafers. A manual cleaving tool has many advantages over a traditional laser-cleaving process. It is more accurate, has more consistency, and is less likely to cause damage to the glass. And it is completely safe. You can safely slice it by hand. This process requires only the use of a laser.
The backside cleaving process is similar to that of the manual cleaving method. It involves cutting the silicon chip into smaller segments. A conventional anodically bonded glass/silicon wafer is divided into two pieces. The size of each chip is 4280x5500 m2. The width of the silicon anchor is 500 m. The length of the glass chip is 900 m.
To dice Fused Silica wafers, I first glued the glass to the silicon wafer using a manual cleaving tool. This tool was designed with ruled markings and provided a convenient way to slice the glass. Once the glue dried, the silicon chips were diced into individual test chips. These devices will be used in the semiconductor industry. A manual cleaving tool is useful for a number of applications.
This manual cleaving method is useful for a number of applications. It can be used to manually dice silicon and glass wafers. The tool can be a good investment if you're a chemist. The manual cleaving tool can help you avoid mistakes. The software has many other features to help you process your glass and silicon. Its user-friendly interface makes it easier to work with.
This manual cleaving tool has a very high precision. Its cribing tool is fully programmable and equipped with a microscope and video to ensure accurate alignment. We have processed all types of glass, fused silica, and compound semiconductors. We also offer custom dicing. A full range of tools is available for your project. And, as a result, cleaving your glass and silicon wafers can be a fast, cost-effective way to produce semiconductors.
For the purpose of manufacturing, you can opt for the standardized method of slicing. The manual process is an option for the production of high-quality crystalline silicon. For example, a manual slicing process can be used for slicing ultra-thin silicon wafers. It also can be used for more complex processes, such as laser etching. Ultimately, you will need to manually dice your wafers in order to manufacture a semiconductor.